زنگ خطر مصرف بالای انرژی در صنایع / انرژیهای تجدیدپذیر حلقه مفقوده صنعت
در تمامی دنیا صنایع برای مدیریت مصرف انرژی بر روی انرژیهای تجدیذیر سرمایهگذاری کردهاند تا مرزهای هشدار را رد نکنند.
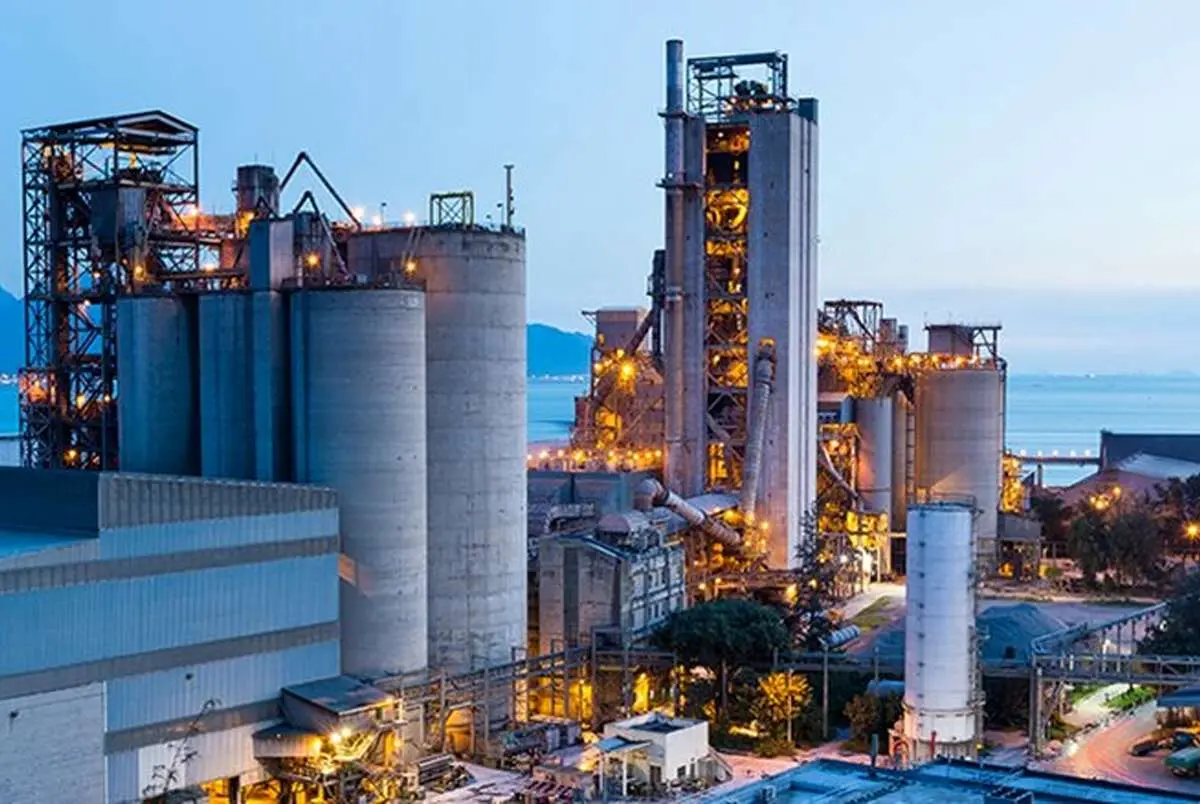
به گزارش اکونگار، صنایع جهان به دلیل تکیه بر تکنولوژیهای نوین نیاز جدی به برخی مواد اولیه دارد. مهمترین این مواد اولیه نفت، کامودیتیها و فلزاتی مانند مس، نیکل، فولاد و لیتیوم هستند. نیاز به این مواد به عنوان اجزاء اصلی تولید، صنعت و انتقال و ذخیرهسازی برق، وسایل نقلیه الکتریکی و زیرساختهای انرژیهای تجدیدپذیر روز به روز بیشتر میشود.
ذخایر معدنی تامین کننده مواد اولیه محصولات فناورانه
شاید برای عدهای غیر قابل درک باشد که چطور ارتباط تنگاتنگی میان صنعت معدن و صنایع فناورانه وجود دارد، اما واقعیت این است که صنایع فناورانه به نیکل، مس و لیتیوم نیاز جدی دارند. این مواد در محصولاتی مانند موبایل، تبلت، کامپیوتر و ساخت تجهیزات این چنینی بسیار کاربردی هستند. در نتیجه میتوان گفت مواد معدنی در ساخت تجهیزات فناورانه موثر است. بیشترتراشههایی که در موبایلها و محصولات حوزه آی تی تولید میشود از مس ساخته شده است. با چنین تفاسیری میتوان گفت که صنعت معدن منابع ضروری تولید در جهان را تامین میکند.
تجهیزات، پرمصرفترین ابزارهای صنعتی
مسله انرژی در جهان روز به روز مهمتر و این روزها حیاتیتر و حتی به مرز هشدار رسیده است. تمامی صنایع جهان تحت تاثیر بحرانهای انرژی با مشکل رو به رو شدهاند. تحقیقات صورت گرفته در موسسه مکنزی نشان میدهد که صنعت نفت نسبت به سایر صنایع انرژی کمتری استفاده میکند، اما صنایع غذایی، صنایع فناورانه، صنایع خودرویی بدون واسطه و با واسطه سهم بالایی در مصرف انرژی دارند و صنعت یکی از پرمصرفترین صنایع جهان در حوزه انرژی صنعت معدن است.
تحقیقات صورت گرفته در موسسه مکنزی نشان میدهد که معادن بین ۳تا ۶درصد از کل برق جهان را مصرف میکنند و بر اساس آمار موجود تا پایان سال ۲۰۲۲ نزدیک به ۶۰ درصد از انرژیهای مصرفی در معادن به تجهیزات و ماشینآلات معدنی بازمیگردد. البته تجهیزات و ماشینآلات در سایر صنایع هم در صدر مصرف انرژی قرار دارند، اما تجهیزات معدنی بسیار پرمصرف شناسایی شدهاند.
بیشتر تجهیزات هم در زمینه خردایش مواد معدنی به منظور کوچک کردن و کم حجم کردن مواد جهت حمل و نقل آسان، خرید و فروش بهتر و راحتتر مواد معدنی و استخراج کانیهای با ارزش از دل مواد معدنی و در بخش استخراج به کار گرفته میشوند. در نتیجه باید گفت که تجهیزات مرتبط با خردایش و استخراج بزرگترین مصرف کننده انرژی نهایی در عملیات معدنکاری هستند.
اما واقعیت این است که با وجود فناوریهای نوین در مراحل استخراج و خردایش مواد معدنی میتوان از یک چهارم کل انرژی نهایی در معدن استفاده کرد و صرفه جویی نسبتاً زیادی در مصرف انرژی و انتشار گازهای گلخانهای داشت.
یک پروژه تحقیقاتی در شرکتهای معدنی استرالیایی که در زمینه سنگآهن فعالیت میکنند، نشان داد که به کمک فناوریهای نوین در مراحل مختلف خردایش مواد معدنی بهبود 5 درصدی در بهرهوری انرژی صورت گرفته و منجر به کاهش انتشار گازهای گلخانهای بیش از 30 میلیون تن CO2-e2 میشود. این تحقیق نشان میدهد اگر راندمان تولید به کمک فناوریهای نوین ۳۵درصد افزایش پیدا کند، در مصرف انرژی هم ۳درصد صرفهجویی در سطح جهان اتفاق میافتد.
واقعیت این است که صنعت معدن به طور کلی مصرف کننده قابل توجهی از انرژی است. برای رویارویی با چالش کربنزدایی، واضح است که صنعت معدن نیاز به تکامل فناوری و تکنولوژیهای روز دنیا در این بخش دارد. در نتیجه نیاز است تا سیستمها و فرآیندهای قدیمی با فناوریهای جدید کارآمدتر و پایدارتر جا به جا شوند.
فرصتهای کاهش مصرف انرژی در صنایع
در سراسر جهان برنامهها و قوانین متعددی برای مدیریت مصرف انرژی تدوین شده است، اما بیشتر صنعتگران به خصوص در صنایع خرد به دلیل هزینههای بالای ورود به حوزه انرژیهای نوین و همچنین ارزان بودن انرژی در برخی از کشورها ترجیح میدهند از انرژی فراوان و ارزان قیمت استفاده کنند.
فرصتهای قابل توجهی برای کاهش مصرف انرژی در صنایع وجود دارد. این فرصتها شامل بهینهسازی مصرف انرژی به کمک تجهیزات و ماشینآلات به روز، استفاده از ظرفیتهای دادههای بزرگ(BigData)،استفاده از پلتفرمهای هوش مصنوعی در صنایع، جایگزینی تجهیزات سنتی خرد کردن با فناوری جدید، یادگیری ماشین و ... هستند.
برای مثال، تجهیزات و ماشینآلات صنعتی و معدنی در جریان فعالیت و یا استخراج و انجام عملیات معدنی فرسود، قدیمی و ناکارآمد میشوند. در نتیجه هزینه عملیات و مصرف انرژی به طرز قابل توجهی افزایش پیدا میکند. استفاده از تجهیزات مدرن و بهرهگیری از فناوریهای روز در تجهیزات معدنی به طور مستقیم بر کاهش مصرف انرژی تاثیرگذار است.
برای مثال متههای مورد استفاده در معادن به کمک هوش مصنوعی میتوانند مناطق مستعد را شناسایی کرده و عملیات معدنی را بین ۵ تا ۲۵درصد بهبود ببخشند. نکته جالب اینجاست که استفاده از این تجهیزات میزان مصرف انرژی در مراحل مختلف استخراج را بین ۶ تا ۱۴ درصد کاهش میدهد.
رشد نوآوری در صنایع جهان
موسسه مکنزی در گزارشی اعلام کرد، در سالهای اخیر کشورهای استرالیا و کانادا سرمایهگذاریهای فراوانی بر روی فناوریهای جدید در صنایع داشتهاند. همزمان با پایان سال ۲۰۲۱ اتحادیه اروپا در گزارشی اعلام کرد که سرمایهگذاری بر روی استارتاپهای صنعتی در تمامی بخشها رشد کرده است و به همین دلیل در میان ۱۶۲ استارتاپ موفق سال، فقط ۵ استارتاپ معدنی و ۸ استارتاپ صنعت غذا در صدر قرار گرفتهاند. همین موضوع نشان از نیاز جدی صنایع حهان به تکنولوژیهای جدید، فناوریهای نوین و روشهای خلاقانه را نشان میدهد.
نقش فناوریهای اطلاعاتی پیشرفته در مدیریت انرژی صنایع
شرکتهای صنعتی و کارخانههای پیشرو به کمک فناوریهای اطلاعاتی پیشرفته (IT) بهبود فرآیندها و به طور همزمان کاهش مصرف انرژی و هزینههای عملیاتی را آغاز کردهاند. صنایع با حجم زیادی از دادهها با لایههای دانش سروکار دارد. از آنجایی که تجزیه و تحلیل داده شامل علم تجزیه و تحلیل دادههای خام برای یک فعالیت صنعتی و رشد اطلاعات است، این یک تکنیک بسیار موثر برای گردآوری منابع دادههای متفاوت به شمار میرود. علاوه بر این، تجزیه و تحلیل دادهها باعث صرفه جویی در هزینه، تصمیمگیری سریعتر و بهتر، و توسعه محصولات و خدمات جدید، میشود. مقدار انرژی مصرف شده توسط یک صنعت، بستگی دارد.
معادن چقدر سوخت مصرف میکنند؟
نوع سوخت یک معدن بسته به نوع آن (معدن زیرزمینی یا روباز) و فرآیند عملیاتهای معدنکاری متفاوت است. در عملیات معدنی از سوخت دیزل، برق، گاز طبیعی، زغال سنگ و بنزین استفاده میشود که به ترتیب 34، 32، 22، 10 و 2 درصد از کل مصرف انرژی را تشکیل میدهند.
بررسیهای نشان میدهد که بیشترین انرژی در جابجایی مواد توسط تجهیزات دیزلی (17 درصد) در صنایع و تجهیزات خردایش مواد معدنی (40 درصد) استفاده میشود.
مصرف بالای انرژی با سیستمهای تهویه و خنککننده در صنایع
سیستمهای تهویه و خنککننده صنایع یکی دیگر از بخشهای پرمصرف انرژی هستند. مراحل مختلفی در طول طراحی، اجرا و بهرهبرداری از سیستمهای تهویه و خنک کننده صنایع وجود دارد که در آنها باید بهرهوری انرژی را بهینه کرد. مرحله اولیه برنامهریزی و بهینه سازی متغیرهای اولیه برای سیستم پیشنهادی است. در مرحله بعد، اجزای سیستم به طور بهینه طراحی میشوند و به دنبال آن یکپارچه سازی کارآمد این اجزا انجام میشود. در نهایت، بهرهوری انرژی در حین کار از طریق کنترل چرخهای سیستمها و در نهایت با تامین تهویه و سرمایش بر حسب تقاضا بهبود مییابد.
بسیار مهم است که اطمینان حاصل شود، اجزاء تهویه و خنک کننده در صنایع(پنکهها، پمپها، کمپرسورها و غیره) به طور مناسب طراحی و تجهیزات کم مصرف تهیه شدهاند، کاهش هزینههای عملیاتی به طور قابل توجهی مستلزم بهینه سازی کلی سیستم است.
مهندسی و بهرهبرداری از سیستمها طی چند دهه به وضعیت فعلی تکامل یافته و دستاوردهای قابل توجهی در بهرهوری انرژی منجر شده است.
افزایش هزینههای تهویه و خنک کننده صنایع به طور ایمن و کارآمد حکم میکند که اپراتورها استراتژیهای مدیریت و کنترل انرژی بهینه را در صنایع اجرا کنند. راهبردهای تهویه بر حسب تقاضا و سرمایش بر حسب تقاضا، پتانسیل کاهش سرمایه و هزینههای عملیاتی سیستمهای تهویه و خنک کننده هر صنعتی را دارند و مکانیسمهای مورد نیاز از نظر فنی در بیشتر صنایع جهان امکانپذیر هستند.